Indice
Come abbiamo analizzato nell’articolo precedente, l’essenza di un vero e proprio sistema Pull sta nel limitare il Work in Progress.
Limitare il WIP porta una serie di benefici che hanno reso obsoleto il sistema Push, in molti contesti. Ma la differenza è davvero così significativa? Cosa cambia realmente nella vita quotidiana dello stabilimento? Cosa cambia per i titolari, per i responsabili di produzione, per gli operai, per i processi produttivi?
L’importanza dell’inventario per la performance
Se di solito negli indicatori di performance vogliamo vedere numeri alti (produttività), o numeri bassi (costi, difetti, tempi di consegna), nella performance dell’inventario la storia è diversa.
Un indicatore molto alto, o molto basso, può creare problemi, come ad esempio quando il magazzino contiene troppe parti che non sono davvero necessarie, o troppo poche quando servono.
Quando l’inventario è troppo grande
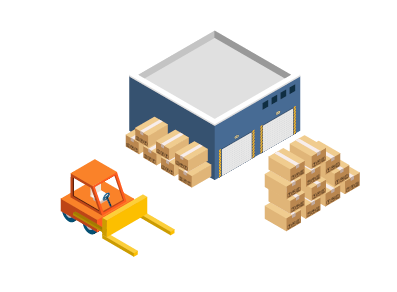
La scorta troppo alta è uno degli sprechi (muda) affrontati nella produzione lean. I costi, chiaramente, salgono alle stelle, il problema è più esteso di quello che sembra.
Problemi tipici di aziende con scorta, inventario, stocks troppo grandi sono:
- capitale bloccato
- complessità di storage
- più spostamenti dei materiali
- tasse e assicurazione
- problemi amministrativi
- obsolescenza
- furti
Per di più, scorte “gonfiate” rallentano la produzione. Se la domanda del cliente è costante e si va ad aumentare il Work In Progress, tutte le parti richiedono più tempo prima di poter raggiungere il cliente (per chi vuole approfondire: legge di Little). Quindi, nuovi prodotti impiegheranno più tempo per raggiungere il mercato, perché il lead time in presenza di scorte alte si alza.
Purtroppo, le aziende non possono più permettersi ritardi nelle consegne, ma scorte alte possono generare spese e ritardi.
Si può ovviare a questo tramite una estensiva riduzione dell’inventario, ma questa soluzione spesso porta con sé altri problemi.
Quando le scorte sono troppo piccole
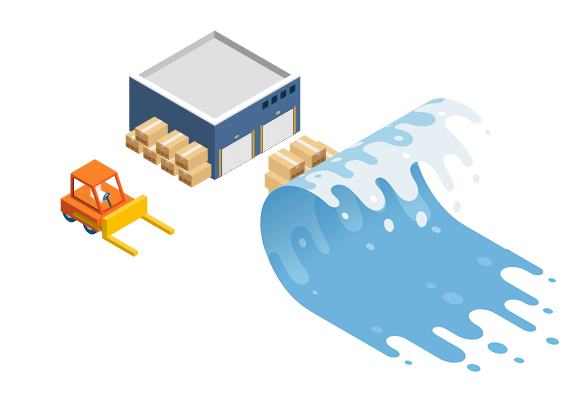
Ogni sistema produttivo tende a “oscillare”. Dovendo produrre prodotti diversi, servono parti diverse, che a volte arrivano troppo presto o troppo tardi. I processi richiedono a volte troppo tempo, altre volte finiscono in anticipo, e certi operatori specializzati non sono sempre disponibili.
Anche il materiale “oscilla”, pensatelo come le onde del mare, il flusso non è costante perchè il materiale arriva a ondate, momenti in cui arriva tutto insieme, seguiti da un periodo più tranquillo, soprattutto se si è alla “fine” della catena, effetto noto come Forrester, Bullwhip, frusta.
L’organizzazione delle scorte è lo strumento chiave per combattere contro questa domanda fluttuante, perché queste “ondate” sono assorbite da scorte “polmone” o “buffer”, che permettono quindi alle macchine e agli operatori di lavorare a velocità costante, indipendente dalla domanda del mercato.
Chiaramente, se si va semplicemente a tagliare il livello delle scorte, si crea un problema, perché non si hanno più le parti necessarie per attutire queste fluttuazioni, e ci si trova semplicemente senza parti quando la domanda sale in modo imprevisto.
Oltre alle scorte, si può usare anche la capacità come seconda misura di difesa. Ovvero, si aumenta la capacità, ma solo quando è necessario, e la si riduce quando non lo è. Tuttavia, questo è difficile su breve preavviso, in un ambiente di produzione moderno e volatile. Non sempre, inoltre, si può avere una sovra capacità senza costi. Una sovra capacità potrebbe essere onerosa, e ricorrere a forniture esterne potrebbe causare altri problemi.
Mancanza di reali soluzioni
Se non si può usare l’inventario o la capacità per gestire queste variazioni, ci si trova costretti a usare una risorsa fin troppo preziosa: il tempo. Più si taglia l’inventario, più si abbassa la velocità di produzione e di utilizzazione, a causa di possibili interruzioni. Questo rende i costi fissi più significativi, perchè le macchine sono ferme, in attesa dei pezzi, e quindi non producono e non rendono.
Se si riduce troppo l’inventario, l’efficienza scende e i costi fissi “salgono”. Questo facilmente diventa più dispendioso rispetto a gestire una scorta di buffer. Inoltre, per forza di cose, l’inventario non si ridurrà più di tanto in ogni caso. Se al sistema manca capacità interna a causa di mancanza del materiale, ma si ordinano comunque parti come se si fosse a piena capacità, ci si ritrova comunque con pile di materiale, eccetto che è quasi tutto quello sbagliato. Se servono 100 parti per fare un prodotto, e se ne possiede 99 ma ne manca 1, le 99 parti potrebbero restare bloccate in giacenza, perché non possono essere utilizzate.
Quando l’inventario è esattamente come dovrebbe essere
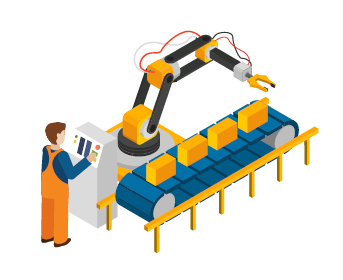
Esiste una via di mezzo dove l’inventario, gestito al meglio, rende il costo minimale e non va a rallentare la produzione.
Chiaramente, vogliamo un inventario che non abbia troppi pezzi, ma neanche troppo pochi, e che soprattutto contenga i pezzi giusti. E questo non è semplice, è impossibile da calcolare con precisione, ma è possibile avvicinarsi molto. Per finire, non esiste un “giusto” numero di parti che resta lo stesso in qualsiasi momento, perché la situazione è variabile e cambia continuamente, anzi è consigliabile usare invece un “range”, così da poter accomodare piccole variazioni.
Molte compagnie hanno capito che il sistema di produzione Lean significa ridurre l’inventario, ma spesso non si accorgono che anche il sistema di gestione va migliorato. Ci sono tentativi di Lean che riducono l’inventario eccessivamente, o che lo riducono quando in realtà andava aumentato.
Le scorte vanno gestite in relazione al tipo di produzione e alla ripetitività, allora in certi casi può essere preferibile avere dei supermarket (linee di montaggio), o concentrarsi sulle materie prime (lavorazione di lamiere), o disporre dei magazzini di disaccoppiamento (post ponement), o ancora impostare delle tecniche VMI (Vendor Management Inventory) o Consignement Stock.
I vantaggi della produzione Pull
Il Pull limita il WIP
Il punto centrale della produzione Pull è di limitare il Work In Progress. Come ho spiegato nell’articolo precedente, la differenza tra Push e Pull , avere un limite massimo sul Work in Progress aumenta la performance e permette ai sistemi produttivi di tenere le scorte esattamente ai livelli ottimali. La situazione si complica quando il lead time di mercato è basso e la variabilità è alta.
Il limite al WIP è automatico
Un sistema Pull crea un sistema automatico che tiene l’inventario sotto a un certo limite, non importa se si implementa il Pull usando il kanban (generalmente alto volume, bassa varietà), o il Continuous WIP (volume basso, alta varietà), o una qualche combinazione, o persino il drum buffer rope.
Se il sistema funziona, serve poca manutenzione per controllare che non siano andati persi alcuni cartellini o per aggiornare il numero di cartellini che il sistema deve controllare.
Adatto per….
Il sistema Pull si adatta facilmente alle linee di montaggio, purché non ci siano componenti ad alto lead time di fornitura, si adatta a prodotti che passano da grezzo a lavorato, e in generale dove c’è una significativa ripetitività. Anche in presenza di prodotti a catalogo, si presta bene per controllare i componenti da montare ad esempio. Nelle lavorazioni per commessa, con scarsa ripetitività, o con semilavorati ingombranti, invece, potrebbe risultare molto difficile se non impossibile determinare dei cartellini, meglio concentrarsi sulle materie prime. Non c’è una regola comunque, e va studiato caso per caso. Il significato di cartellini non deve essere inteso letterale (di carta), possono benissimo essere elettronici, o gestiti da mrp con politica opportunamente e correttamente impostata.
Il sistema Pull correttamente impostato è davvero adattabile ad ogni realtà produttiva, purché i livelli di scorta ed anche il posizionamento della scorta stessa sia valutato con attenzione.
Dopo questa (lunga) introduzione, si possono capire quindi i limiti di quanto asserito qui di seguito.
L’inventario può fluttuare, ma non è un problema
Tenete a mente che, sebbene il WIP sia limitato in modo fisso, l’inventario non lo è, e può fluttuare. Ad esempio, in un sistema kanban, in via teorica potremmo avere tutto il kanban fermo nel supermarket, insieme al materiale associato, e allo stesso tempo raggiungere il massimo WIP. Tuttavia, è anche possibile che tutti i cartellini stiano aspettando la produzione, e il nostro WIP sarebbe zero. Naturalmente, la realtà sta nel mezzo.
Questo tipo di fluttuazione non è un problema. La formula kanban e l’approccio di stima kanban alternativo determina il numero di cartellini necessari per operare in modo puntuale, ma il WIP medio sarà spesso più piccolo della somma dei cartellini kanban.
È un sistema robusto
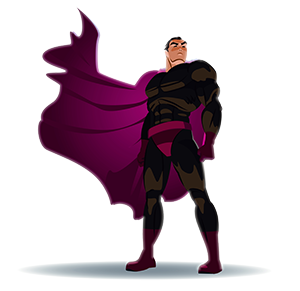
Ci sono altri modi di controllare la produzione. Si può ad esempio pianificare usando la capacità disponibile e le deadline stabilite, che è l’approccio convenzionale push.
Purtroppo sia la capacità che le deadlines tendono a essere molto volatili e cambiare rapidamente. Per questo, pianificare in anticipo è molto difficile, e i frequenti cambi al piano di produzione possono far perdere molto tempo e creare complicazioni. È difficile gestire la produzione push.
Nella produzione Pull, una volta stabilito il limite della WIP, e possibilmente dopo aver prioritizzato quale parte produrre in seguito, non è necessario pianificare la capacità nel dettaglio. Le deadline sono più semplici da gestire, perchè il sistema è più rapido. In più, il sistema tende a essere più robusto.
Non importa se il limite è troppo alto o troppo basso, in generale il sistema funzionerà comunque, anche se non si va a colpire il limite WIP più preciso. La produzione Pull è in generale molto robusta e resistente alle fluttuazioni nel sistema.
Siamo a vostra disposizione
Per chiarimenti o consulenze, se hai problemi di qualsiasi tipo relativi alla produzione, contattaci su LinkedIn o tramite email a paolo.tiso@factorysolver.it
Saremo lieti di essere la tua risorsa di fiducia per la gestione della produzione, per sistemi MES, e per ERP/MRP.
Con 30 anni di esperienza combinata tra me e Michele, Factory Solver vive e respira la produzione.