Indice
Un buon metodo per tenere sotto controllo il numero di kanban è di partire da un numero più che sufficiente di cartellini, e poi vedere se si può ridurli. Qui vogliamo spiegare come funziona questo approccio, e come e quando cambiare il numero dei kanban.
Per un approfondimento su formule e dettagli, vi preghiamo di leggere l’ultimo paragrafo.
Partire con una stima semplice dei Kanban
Invece di calcolare il numero di kanban usando formule complesse, possiamo stimare quanti ne saranno necessari con una formula semplice (per un approfondimento, leggere l’ultimo paragrafo). Per fare questo serve esperienza, e raccomandiamo di non farlo senza l’aiuto di un supervisore o un caposquadra del relativo shop floor.
Naturalmente questa è soltanto una approssimazione, si deve scegliere un numero leggermente abbondante, per essere sicuri che avrete sufficienti cartellini. Chiaramente, attenzione a non bucare il budget.
Se il lead time di mercato è “stretto”, è preferibile avere un eccesso di parti che trovarsi carenti, con possibilità quindi di avere lavoratori in attesa o spedizioni mancate. Una delle colonne della filosofia lean si basa sulla riduzione degli sprechi, quindi dovremmo evitare immobilizzazione di materiale, e anche di avere materiale non ancora richiesto, d’altra parte con le oscillazioni attuali per i settori poco ripetitivi avere il materiale da lavorare è fondamentale, non possiamo essere senza.
Una volta che il nostro sistema kanban è operativo, passiamo a verificare che il numero di kanban sia ottimale.
Controlliamo che i Kanban siano giusti per il sistema
Come si può verificare se il numero di kanban si abbina al nostro sistema in modo ottimale?
Ipotizziamo di avere strutturato dei supermarket. Come prima cosa dovremmo tracciare l’andamento nel tempo della quantità nei supermarket. Nel caso migliore, si avrà una distribuzione come si può vedere qui sotto. Il grafico mostra l’inventario per un tipo di prodotto nel supermarket, che può variare tra zero, quando manca lo stock e il massimo di tutti i kanban presenti nel supermarket. Il grafico qui sotto sarebbe una distribuzione ideale. Non si è mai senza stock, e siccome il supermarket non è mai pieno, non si è mai senza lavoro.
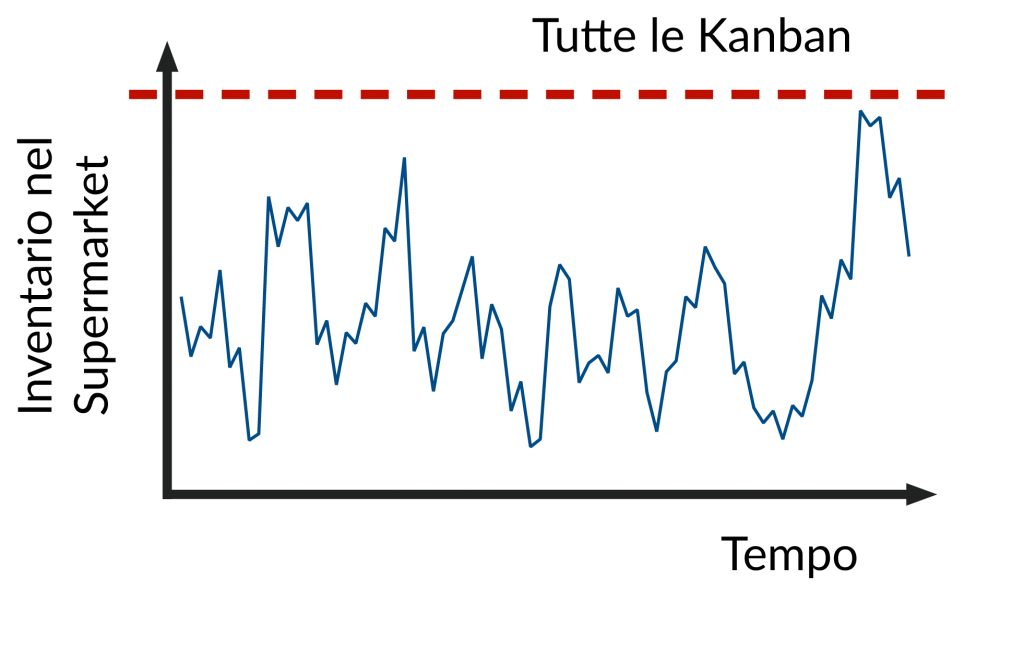
A volte può capitare di toccare sia il limite massimo che quello minimo. Toccare il limite massimo non è un problema, specialmente se si lavora in batch di grandi dimensioni. In tal caso il grafico potrebbe assomigliare a quello qui sotto.
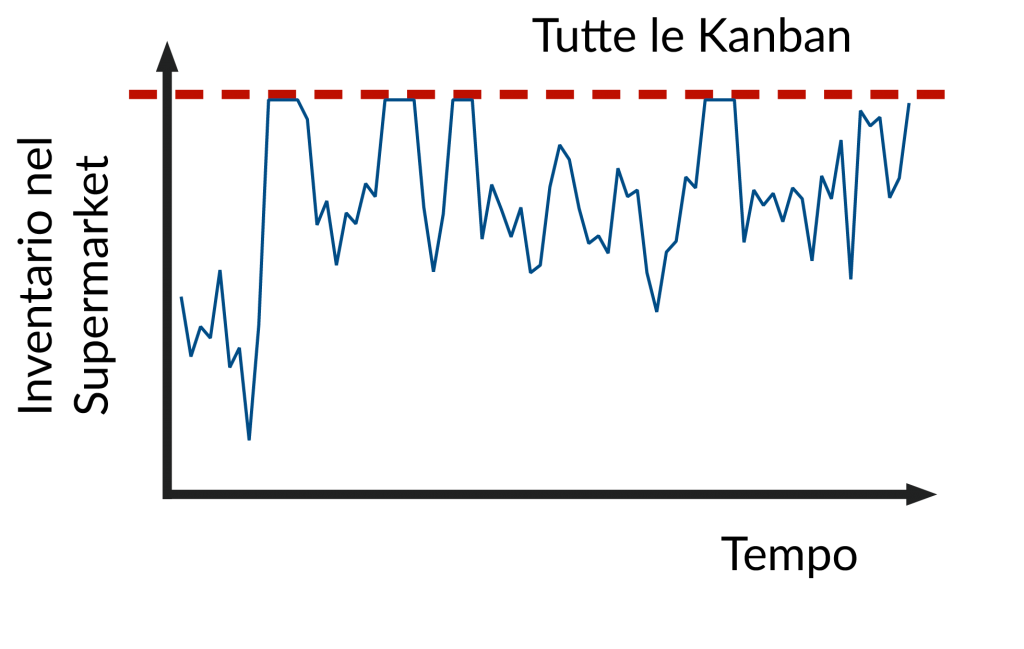
Raramente però, può succedere di trovarsi senza stock.
Nell’esempio qui sotto, il sistema si è trovato senza stock solo una volta durante il periodo di osservazione. Naturalmente, più kanban avrebbero fatto da tampone e avrebbero impedito di restare senza stock. In questo scenario, occorre decidere se vale la pena aggiungere altri kanban.
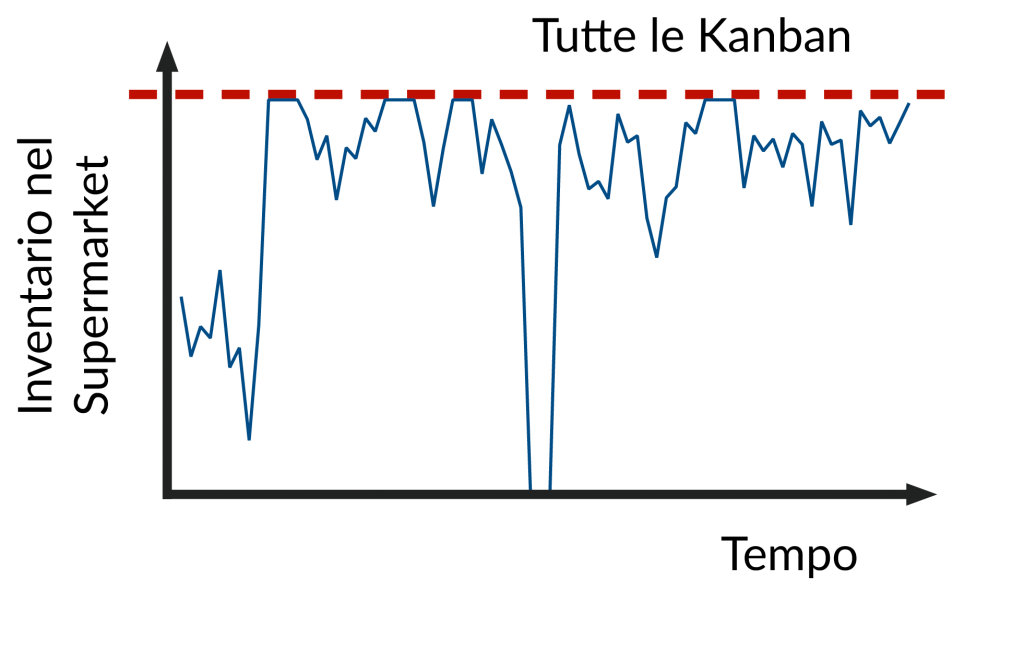
Se accade molto raramente, si può decidere di tenere le cose come stanno, piuttosto che aumentare gli stock.
Se invece l’andamento assomiglia di più a quello qui sotto, allora ci si sta avvicinando alla soglia pericolosa dell’assenza del materiale, con potenziali conseguenze negative sul servizio, non ci sono sufficienti kanban.
E’ probabile che in presenza di un grafico simile, presto il cliente si farà sentire.
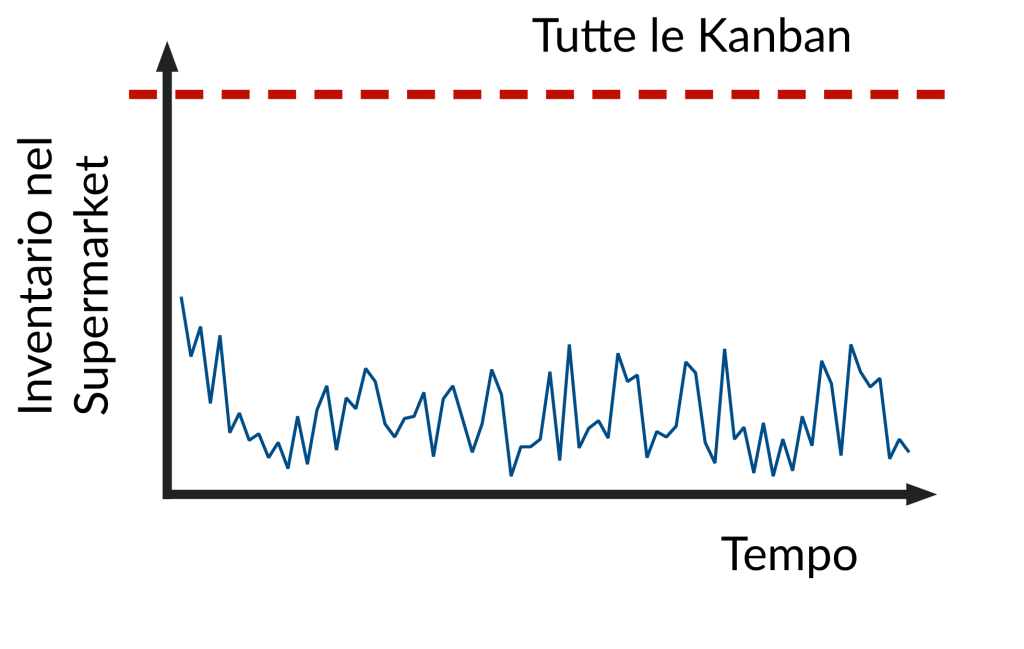
Altra possibilità: può accadere di avere uno stock sempre vicino al massimo, cioè tutti i cartellini sono quasi sempre disponibli. In questo caso ci dobbiamo chiedere se non abbiamo troppi kanban. Dovremo premdere in considerazione l’idea di ridurne il numero per avvicinarcu di più alle situazioni nella nostra prima o seconda immagine.
Il numero totale di kanban che si potrebbero rimuovere sono un po’ meno della differenza tra l’inventario più basso e lo zero. Ad esempio, nell’esempio sottostante, basterebbero in teoria metà kanban. Naturalmente, è consigliabile cominciare con cautela e rimuoverne magari un quarto.
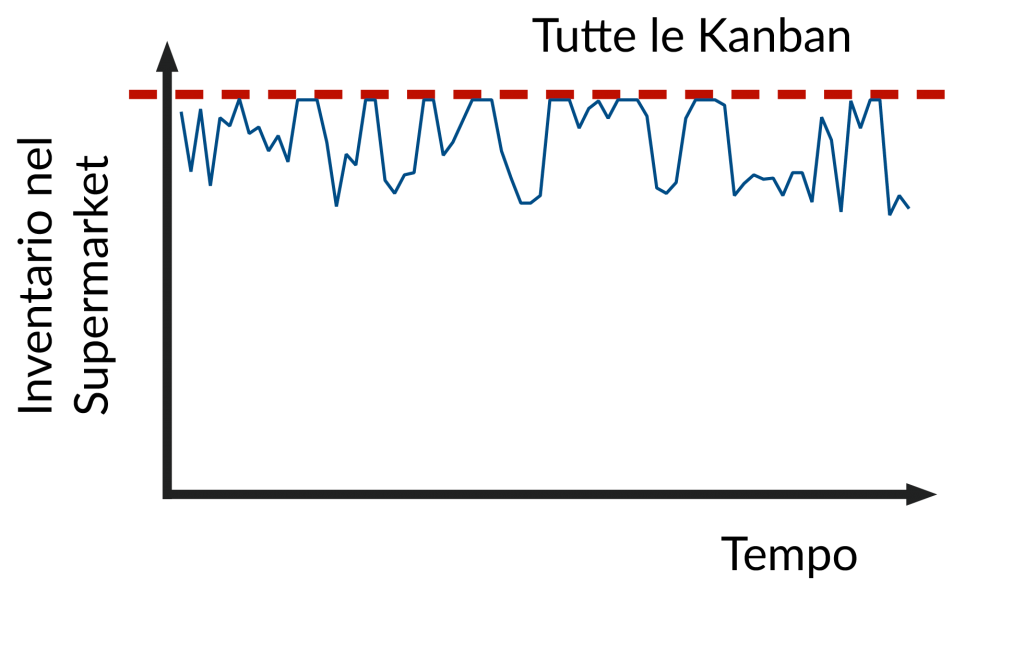
Poi continuiamo ad osservare, e valutiamo se aggiungere o rimuovere kanban.
Se stessimo parlando di MRP, invece, diremmo che periodicamente vanno rivalutati scorta minima, percentuale per calcolo della sicurezza e lotto di riordino: la dinamicità attuale richiede di aggiornare spesso i dati.
Detta in breve, si dovrebbero osservare gli andamenti degli inventari dei supermarket, per decidere se aumentare o diminuire il numero dei kanban, sfruttando dati accurati provenienti dal mondo reale, e confrontando con le formule kanban. E’ consigliabile controllare sempre i risultati e confrontare ipotesi e realtà.
Se ci si trova senza cartellini, nonostante il calcolo kanban, chiaramente non ci sono sufficienti kanban, e bisogna correggere la situazione, cioè non stiamo ad aspettare di ricalcolare, lasciamo che i cartellini lavorino per noi e diamogli retta.
In un sistema ben funzionante kanban, di solito metà dei contenitori è pieno, e l’altra metà è vuota in attesa del “replenishment”.
Tenere i livelli sott’occhio ogni stagione?
Ripetiamo spesso che i sistemi produttivi sono raramente statici, e che cambiano spesso. Il numero dei kanban di oggi potrebbe non bastare nella prossima stagione. Se abbiamo stabilito un sistema ottimale, dobbiamo comunque tenere d’occhio i risultati di tanto in tanto e assicurarci che la performance resti ottimale.
La stagionalità in particolare tende a rivelare dei pattern evidenti, quando fuori stagione la domanda cala e sono necessari molti meno kanban. In questo caso, basta aggiungere più kanban quando parte la stagione con la domanda più alta, e rimuoverli in seguito.
Approfondimento: Formule
Esistono diverse formule per calcolare il numero di cartellini Kanban necessari. Vedremo di prenderne una tra quelle semplici, metterla in relazione ad una formula mrp, e di valutare qualitativamente un metodo per tenere sotto controllo il numero di cartellini.
Diamo un’occhiata alla formula più semplice per il “Lotto di riordino”.
Lotto di riordino = consumo giornaliero * giorni copertura
Ci ricorda qualcosa? Confrontiamola ora con una formula per trovare il numero di cartellini kanban:
Cartellini Kanban = [ (consumo_medio * giorni_copertura * (1 + K sicurezza) ] / (qtà movimentazione)
Possiamo notare che il numero cartellini non è altro che il lotto di riordino, aumentato di un fattore per aumentare il livello di sicurezza, e diviso per la quantità che ci sta in un cassone, o pallet, o scatola, o altro contenitore.
Si noti anche che si parla di “media” di coefficiente di sicurezza (sigma solitamente): questo comporta che l’articolo sia piuttosto ripetitivo nei consumi, altrimenti è piuttosto difficile e rischioso applicare sia kanban sia politica a riordino. Il coefficiente di sicurezza serve a garantire un maggior servizio al cliente.
Perchè usare kanban invece del lotto riordino?
Presto detto: utilizzando kanban, se il numero di cartellini è almeno superiore a 2, si avranno movimenti di materiale più frequenti e di quantità inferiore, avvicinandosi di più ad un sistema a flusso. Invece con lotto di riordino, lo dice la parola, le quantità che si muovono sono “lotti” e ci si allontana dal flusso.
Il lotto di riordino va solitamente in coppia con la scorta minima, che si calcola come consumo medio giornaliero di ciascun prodotto, in un determinato periodo, moltiplicato per i giorni necessari al riapprovvigionamento, eventualmente aumentata per garantire un maggior servizio. Se ci si basa sulla media, una volta sarà inferiore, un’altra superiore al consumo reale, ed è noto che occorre quindi maggiorare la scorta minima di una percentuale per garantire il servizio. Abbiamo avuto esperienza e dimostrato presso un cliente, che un aumento modesto rispetto alla media (si sfrutta la Gaussiana evidentemente) ha portato la puntualità di consegna da circa 50% a oltre 90% (non istantaneamente, ci sono voluti molti mesi), e si è iniziato a pianificare anche i terzisti, con soddisfazione di tutta la catena, terzisti, acquisti, produzione, clienti.
Abbiamo capito che è fondamentale avere una media: quando il consumo è discontinuo e poco stabile, sarà molto difficile trovare un equilibrio, che si usi mrp o kanban, ma il kanban si adegua più velocemente alle variazioni, perché si muovono più velocemente i cartellini quando il consumo aumenta, e più lentamente quando diminuisce, invece con il solo reorder point si rischia di arrivare al riordino senza rendersi conto se la richiesta è aumentata o diminuita o c’è stato un picco.
Bene, si sia trovato allora un numero di partenza per i cartellini.
Siamo a vostra disposizione
Per chiarimenti o consulenze, se hai problemi di qualsiasi tipo relativi alla produzione, contattaci su LinkedIn o tramite email a paolo.tiso@factorysolver.it
Saremo lieti di essere la tua risorsa di fiducia per la gestione della produzione, per sistemi MES, e per ERP/MRP.
Con 30 anni di esperienza combinata tra me e Michele, Factory Solver vive e respira la produzione.